· Marcel Hahn · Events
16th FVI Expert Breakfast
Innovative Instandhaltung: KI-Lösungen direkt aus der SPS
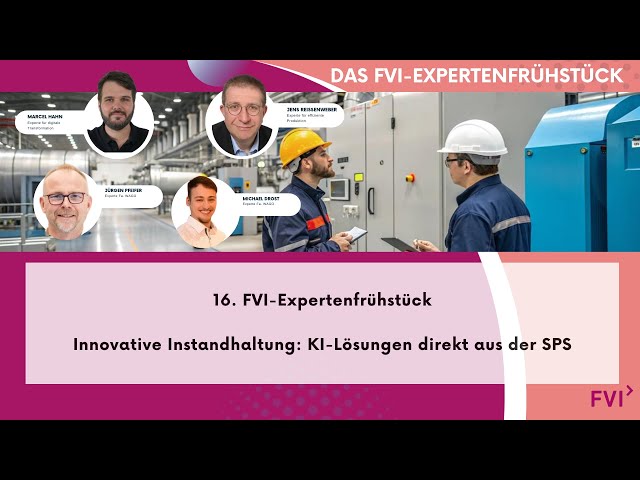
Announcement
We are pleased to invite you to our next FVI Expert Breakfast! On Friday, February 7th, 2025, from 09:30 to 10:30 AM, we will explore the exciting topic: “Innovative Maintenance: AI Solutions Directly from the PLC”.
Join us as we discuss the challenges of today’s IoT projects and discover best practices and the benefits of AI in maintenance.
Our moderators Marcel Hahn and Jens Reissenweber from FVI will guide you through the event, while experts from WAGO, Jürgen Pfeifer and Michael Drost, will share valuable insights and experiences.
Be there live and look forward to an informative hour full of innovative ideas!
🗓 Date: Friday, 07.02.2025
⏰ Time: 09:30 - 10:30 AM
📍 Location: Live on Teams
Fri, Feb 7, 2025 09:30 - 10:30 (UTC+01:00) Amsterdam, Berlin, Bern, Rome, Stockholm, Vienna
We look forward to your participation!
Summary
- Introduction and Presentation:
Jens Reissenweber opens the meeting and introduces the discussion topics. Jürgen and Michael Drost from WAGO present themselves and their roles.- Meeting Opening: Jens Reissenweber opens the meeting and provides a brief overview of the planned discussion topics. He emphasizes the importance of practical implementation of IoT and AI and encourages participants to engage in active discussion.
- Introduction of Jürgen: Jürgen Pfeifer introduces himself and explains that he has been working in the IoT and analytics field at WAGO for many years. He highlights his role in partner management and his enthusiasm for presenting IoT and AI topics.
- Introduction of Michael: Michael Drost introduces himself as a Field Application Engineer at WAGO. He supports customers in using automation products, especially in Northern Bavaria, and mentions his colleagues in other regions.
- IoT and AI in Practice:
Jürgen and Michael Drost discuss the challenges and solutions in implementing IoT and AI in practice. They show a video about an internal solution at WAGO that introduces maintenance staff and employees to AI and machine learning.- IoT Challenges: Jürgen Pfeifer talks about the challenges in implementing IoT and AI, particularly the need for coordination between different departments. He presents a closed solution that is scalable and demonstrates how AI can be used directly from the PLC.
- Internal Solution: A video shows an internal solution at WAGO developed a few years ago in production. This solution introduces maintenance staff and employees from various departments to AI and machine learning.
- Material Distribution System: The presented material distribution system is an in-house development by WAGO that transports granulate to the injection molding machines. The system operates using vacuum pressure, and the extracted dust is collected in a filter to protect the pump.
- Maintenance Intervals: Sebastian explains that traditional maintenance intervals are not always appropriate, as they vary depending on system usage. Sensor data is used to generate knowledge and provide maintenance staff with a digital tool to optimize their work.
- Technical Implementation and Benefits:
Jürgen and Michael Drost explain the technical implementation of the solution, including the use of WAGO components and integration into SAP systems. They highlight benefits such as a 50% reduction in troubleshooting time and optimized processes in terms of energy efficiency and sustainability.- Technical Implementation: Jürgen Pfeifer explains that the system uses WAGO I/O systems and components from the portfolio to establish connectivity to the sensors and perform analytics computing tasks. Connectivity to SAP systems is enabled via the SAP Plant Connectivity Tool.
- Troubleshooting Reduction: The time required for fault localization and troubleshooting was reduced by more than 50%. This was achieved through predictive maintenance and the use of machine learning models that provide early warnings of potential issues.
- Energy Efficiency: Processes are optimized for energy efficiency, contributing to improved quality and sustainability. This includes both the recycling process of plastic materials and the infrastructure of the machines.
- Collaboration: Collaboration between departments was crucial to the project’s success. It was emphasized that good teamwork and a willingness to cooperate are essential for successful analytics implementation.
- Live Demonstration:
Michael Drost performs a live demonstration showing how data can be captured and processed in the familiar PLC environment. He explains the use of function blocks and the integration of machine learning models.- Data Acquisition: Michael Drost demonstrates how data can be captured in the familiar PLC environment. He uses function blocks to leverage the resources of a server or edge computer since the PLC itself lacks the power to run machine learning models.
- Function Blocks: Michael Drost explains the different function blocks used for data acquisition and processing. These include blocks for data acquisition, graphical visualization, and machine learning models such as anomaly and drift detection.
- Machine Learning Integration: Machine learning models are integrated via a library for the PLC. This allows the use of ML models without deep IT knowledge. The models run on an edge computer installed with a click of a mouse.
- Live Data Processing: Michael Drost demonstrates live how data is captured, processed, and visualized from the PLC. He shows how randomly generated values are processed in real-time and displayed on a dashboard.
- Questions and Discussion:
Jens Reissenweber and other participants ask technical questions and discuss potential applications of the presented solution. Concerns and challenges related to the implementation and use of AI and IoT are also addressed.- Technical Questions: Jens Reissenweber and others ask technical questions about the presented solution. They discuss how data can be collected and used to gain insights and optimize processes.
- Challenges: Concerns and challenges in implementing and using AI and IoT are discussed. These include the need for clear objectives, coordination between departments, and integration into existing systems.
- Data Analysis: Participants discuss various approaches to data analysis. It is emphasized that both targeted data collection and gathering all available data are valid approaches depending on specific requirements and goals.
- Funding Opportunities: Kurt speaks about funding opportunities for software and asks a specific question about applying the presented solution in an energy project. Jürgen and Michael Drost offer to discuss the topic further in a personal conversation.
- Funding Opportunities and Project Ideas:
Kurt discusses software funding opportunities and asks a specific question about applying the presented solution in an energy project. Jürgen and Michael Drost offer to explore the topic further in a personal conversation.- Funding Opportunities: Kurt talks about the possibility of receiving 25% funding for software. He considers how this could be used in an energy project to apply and analyze the presented solution.
- Personal Discussion: Jürgen and Michael Drost offer to discuss the topic further in a personal conversation to address specific questions and application possibilities in the energy project.
- Error Analysis and Prevention:
Peter asks about the experiences and the claim that troubleshooting time can be reduced by 50%. Michael Drost explains how AI helps with filter monitoring and detecting leaky valves, which significantly saves time.- Troubleshooting Reduction: Michael Drost explains that troubleshooting time was reduced by 50% because the AI provides early warnings of potential problems. This was achieved through predictive maintenance and the use of machine learning models.
- Filter Monitoring: AI helps monitor the filters in the material distribution system. It detects early when a filter change is needed, increasing maintenance efficiency and easing troubleshooting.
- Leaky Valve Detection: Michael Drost explains that the AI also helps detect leaky valves in the system. This saves time in troubleshooting as the AI pinpoints the leak instead of requiring a manual search.
- Cultural and Organizational Challenges:
Christian and Christoph discuss the cultural and organizational challenges in implementing AI and IoT. They emphasize the need for a culture of openness to errors and the importance of clear goals and project organization.- Open Error Culture: Christian stresses the importance of an open error culture to foster innovation. He explains that mistakes should be seen as learning opportunities and that a culture of experimentation is necessary for successfully implementing modern technologies.
- Goal Setting: Christoph highlights that clear goals and structured project organization are essential for successful project implementation. Without concrete goals and good organization, many projects remain in the comfort zone and fail to progress.
- Management Responsibility: Christoph explains that implementing AI and IoT is a management responsibility requiring experience and commitment. It is important to build teams, ensure transparency, and inspire employees about new technologies.