· Marcel Hahn · Events
18th FVI Expert Breakfast
Global Maintenance KPIs – Curse or Blessing?
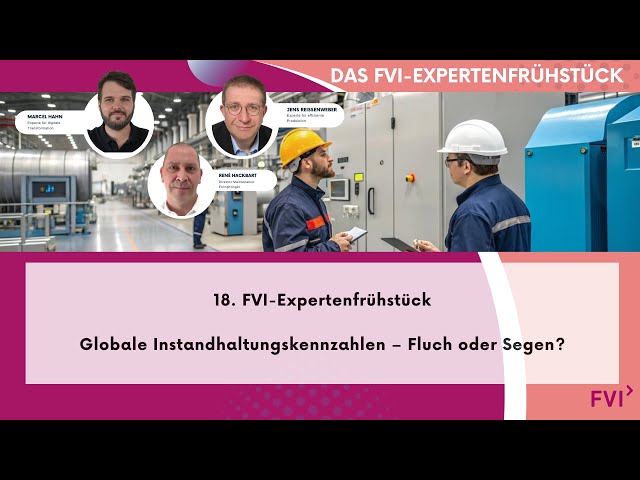
Announcement
Global Maintenance KPIs – Curse or Blessing?
Which data is truly helpful, and which only creates confusion?
“Implementing a Global KPI System for Maintenance” – this is the topic of the 18th FVI Expert Breakfast, where René Hackbart, Director Global Maintenance at ElringKlinger, will showcase how a global KPI system was successfully implemented – from early challenges to a functioning rollout.
📅 Friday, March 7, 2025 | 09:30 – 10:30 AM
📍 Online – live & interactive
The 4 Key Topics: 1️⃣ From idea to implementation – Why ElringKlinger needed a global KPI system and what goals were pursued
2️⃣ Major hurdles and stumbling blocks – What didn’t go as planned? Which KPIs actually work?
3️⃣ Less is more – Why only five KPIs are used today and how they were standardized
4️⃣ Exchange & benchmarking – How companies can securely and comparably use KPIs in a new FVI working group
🎙️ Featuring:
René Hackbart, Director Global Maintenance, ElringKlinger
Marcel Hahn & Jens Reißenweber as moderators
This session is not only a behind-the-scenes look at a real industrial project – it’s also the launch of a new FVI working group on KPIs & benchmarking.
Fri, Mar 7, 2025 09:30 - 10:30 (UTC+01:00) Amsterdam, Berlin, Bern, Rome, Stockholm, Vienna
We’re excited to have you join us!
Summary
Introduction and Welcome:
Marcel and René welcomed the participants and spoke about expectations for the session. Marcel mentioned that the session would be recorded and asked attendees to turn on their cameras.Topic Introduction:
Marcel introduced the session topic: “Global Maintenance KPIs – Curse or Blessing?” and announced the guest speaker René Hackbart from ElringKlinger.- Topic: Marcel emphasized the relevance of the topic for the audience and the importance of discussing the pros and cons of global maintenance KPIs.
- Guest Speaker: René Hackbart was introduced as the person responsible for global maintenance at ElringKlinger, highlighting his expertise and experience.
Introduction to the KPI System:
René Hackbart described the initial situation and the requirements for the KPI system at ElringKlinger. He highlighted the need for comparability between sites and consistency of KPIs.- Initial Situation: Before 2017, there was no central maintenance organization at ElringKlinger. A global KPI system was necessary to standardize and compare maintenance across roughly 30 sites.
- Requirements: The system had to be applicable to all sites, compliant with IATF standards, enable cross-site comparability, and deliver consistent KPIs. The goal was to aggregate data globally to derive high-level targets.
- Comparability: René emphasized the importance of being able to compare site performance to improve maintenance globally.
KPI Definition:
René explained how KPIs were defined in regional meetings with site representatives, evaluating them based on data availability and comparability.- Regional Meetings: KPIs were defined collaboratively during regional meetings. A full day was dedicated to discussing which KPIs were meaningful and feasible.
- Data Availability: KPIs were assessed based on whether data came from SAP or had to be collected manually, and whether that data was comparable across all sites.
- Comparability: Only KPIs with consistent data availability and cross-site comparability were selected.
Adjustments and Challenges:
René talked about challenges such as system crashes and manual input errors. The number of KPIs was reduced, and targets for unreliable KPIs were eliminated.- System Failures: System crashes occurred when processing large data volumes, especially with Mean Time Between Failures (MTBF) in large sites.
- Manual Input Errors: Common mistakes included incorrect number formatting (period vs. comma for thousands), leading to faulty data.
- KPI Reduction: The number of KPIs was reduced from 15 to 13. Targets were removed for KPIs with insufficient data reliability to improve overall quality and comparability.
Current Reporting System:
René presented the current reporting setup based on SAP Analytics Cloud using automatically generated data. He shared current KPIs and announced the upcoming inclusion of the Total Maintenance Cost Ratio.- SAP Analytics Cloud: The current system relies on SAP Analytics Cloud and uses automatically generated data to minimize errors and improve data quality.
- Current KPIs: These include Mean Time to Repair (MTTR), Unplanned Maintenance Cost Ratio, Preventive Maintenance Completion Ratio, and Spare Parts Inventory Ratio.
- Total Maintenance Cost Ratio: This KPI will soon be added to reflect total maintenance costs in relation to asset value.
Discussion and Feedback:
Participants asked questions and gave feedback about the KPIs and the reporting system. There was a lively discussion on the difficulties in determining certain KPIs and the role of benchmarks.- Questions & Feedback: Attendees asked about monthly evaluations and how asset value is considered in the metrics.
- Challenges: Issues around determining MTBF and data availability were discussed. René shared experiences on the limitations and improvements made.
- Benchmarks: The importance of benchmarking was highlighted. Anonymized benchmarking was seen as a useful approach to assess performance and identify opportunities for improvement.
Future Plans & FVI Platform:
René and Jens discussed using the FVI platform for sharing KPIs and creating anonymized benchmarks. They stressed the need for unified reporting and the advantages of this kind of exchange.- FVI Platform: The potential for using FVI as a secure platform for KPI sharing and benchmarking was discussed.
- Unified Reporting: A consistent reporting approach would improve KPI comparability and provide a common basis for discussion and improvement.
- Benefits of Sharing: Exchanging KPIs and best practices can help companies learn from one another and improve maintenance processes across the board.