· Marcel Hahn · Events
20th FVI Expert Breakfast
Cat and Mouse – Turning Production and Maintenance into a Dream Team
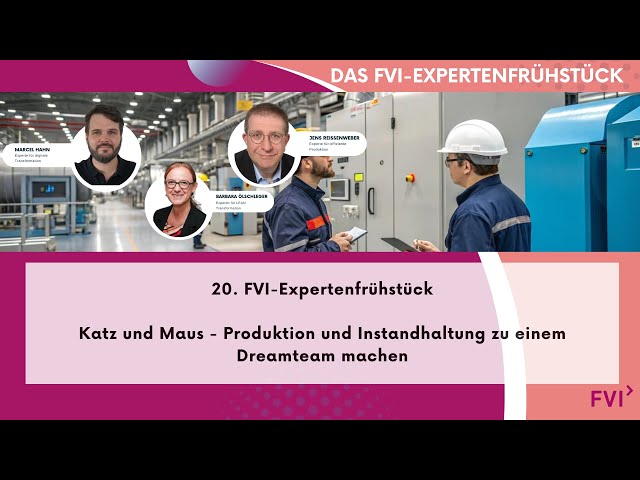
Announcement
“Cat and Mouse – Turning Production and Maintenance into a Dream Team”
📅 When? Friday, April 4, 2025, 09:30 – 10:30 AM
🌍 Where? Online – live & interactive
👥 Moderation & Hosts:
🎤 Marcel Hahn – Expert in Digital Transformation & Moderator
🎤 Jens Reissenweber – Expert in Efficient Production & Moderator
🚀 Our Expert:
➡️ Barbara Ölschleger – Gemba Booster
🎯 What to expect?
We’ll discuss how TPM and success stories can make a difference:
✅ Main Topic: A discussion on the traditional role division between production and maintenance, challenges and solutions in Total Productive Maintenance (TPM), as well as real-world examples for reducing downtime and improving efficiency.
✅ Experiences and Success Stories: Presentation of successful case studies and best practices, discussion of TPM implementation and the role of leadership. A strong emphasis will be placed on TPM, which aims to maximize productivity through preventive maintenance measures. Successful examples show how companies have optimized their production processes through TPM by reducing downtime and increasing efficiency. Leadership plays a crucial role in implementing TPM by motivating employees and providing the necessary resources.
📌 Special Highlight:
Find out how TPM has already been successfully implemented in various companies and which best practices have proven effective.
Fri, Apr 4, 2025 09:30 - 10:30 (UTC+01:00) Amsterdam, Berlin, Bern, Rome, Stockholm, Vienna
We look forward to your participation!
Summary
Registrations for the Event:
Barbara and Marcel discussed the high number of 90 registrations for the event and expressed excitement about the strong interest.Maintenance Issues:
Barbara shared a story about a customer in Switzerland where the maintenance team failed to respond to a scheduled maintenance window, leading to problems.- Maintenance Window: A customer in Switzerland had a 2.5-day maintenance window, which was known to the maintenance team. However, they did not act on it, leading to issues.
- Lack of Response: The maintenance team failed to react despite being informed, which caused significant problems and delays.
- Communication Issues: Barbara emphasized that this is a typical example of communication breakdowns and lack of mutual understanding.
Communication and Leadership:
Barbara and Marcel highlighted the importance of communication and leadership in projects and companies to avoid misunderstandings and friction.- Importance of Communication: They discussed how effective communication is essential to prevent conflicts and ensure smooth project execution.
- Leadership Topics: Marcel noted that many leadership issues are intensified by poor communication, and clear, open dialogue is needed to address them.
- Project Management: Marcel mentioned his background in classic project management and stated that while many methods exist, success ultimately depends on communication.
Company Results:
Barbara presented the results of a company that implemented TPM and saw positive impacts on performance indicators.- TPM Implementation: One company increased technical efficiency by 8% and reduced cleaning times by 30% after introducing TPM.
- Defect Cards: In 2022, 3,837 defect cards were submitted, showing active employee involvement in process improvement.
- Maintenance Success: The Mean Time Between Failures (MTBF) doubled, and the number of breakdowns was halved, significantly boosting maintenance efficiency.
Collaboration Between Production and Maintenance:
Barbara explained how TPM can improve collaboration and which actions contribute to better teamwork.- Autonomous Maintenance: Introducing autonomous maintenance, such as deep cleaning and reporting systems, improves cooperation.
- Increasing Efficiency: Training employees and introducing inspection plans are key measures to boost maintenance performance.
- Leadership Focus: Leaders play a vital role in encouraging collaboration and addressing inappropriate behavior directly.
Leadership Topics:
Barbara emphasized the importance of leadership and how managers should address inappropriate behavior constructively.- Addressing Behavior: Leaders should address inappropriate behavior directly and objectively to foster a positive work environment.
- Strengthening Team Spirit: Managers should emphasize teamwork and clarify that production and maintenance succeed together.
- Maintaining Objectivity: Barbara stressed that leaders should remain objective and keep emotions out of discussions to focus on facts.
Discussion on OEE:
Thomas Bacher and Barbara discussed the importance of OEE as a key performance indicator and its role in shopfloor management.- Importance of OEE: Thomas emphasized OEE as a crucial KPI for shopfloor management. Barbara agreed but added that employees also need specific KPIs they can directly influence.
- Employee Impact: Barbara explained that while OEE is a great guiding KPI, employees need metrics that reflect their daily work to drive real improvements.
Job Rotation and Training:
Roman and Oliver shared positive experiences with job rotation and apprentice training in production to improve cross-department understanding.- Job Rotation: Roman reported that introducing maintenance weeks, where production workers help in maintenance, improved the company culture.
- Apprentice Training: Oliver explained that involving apprentices in both production and maintenance improved mutual understanding between departments.