· Marcel Hahn · Events
21th FVI Expert Breakfast
Rethinking workplace safety – practiced leadership and self-responsible actions instead of just regulations.
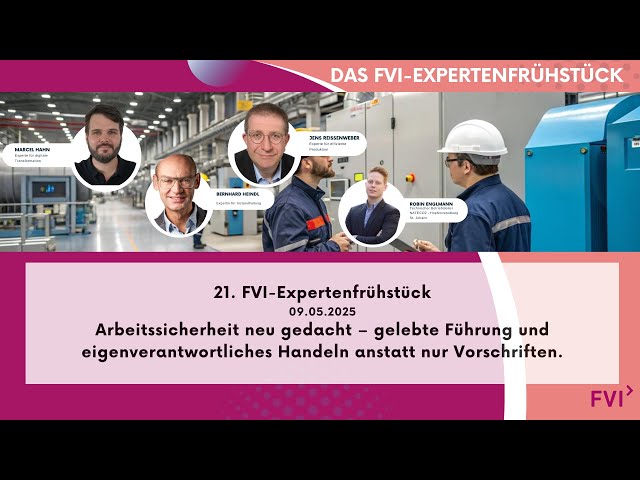
Announcement
Traditional safety instructions: Boring, technical, and quickly forgotten. But workplace safety in maintenance is too important to be reduced to signatures and documents!
At the 21st Forum Vision Maintenance e.V. Expert Breakfast, we will show how modern safety management really works through practiced leadership, self-responsibility, and practical approaches – and why everyone has safety “in their own hands.”
📅 When? Friday, May 9, 2025, 09:30 – 10:30 AM
🌍 Where? Online – live & interactive
👥 Moderators & Hosts: 🎤 Marcel Hahn – Software Expert & Moderator 🎤 Jens Reißenweber – Maintenance Consultant & Moderator
🚀 Our Experts: ➡️ Robin Englmann – Technical Operations Manager, Hopfenveredlung St. Johann GmbH ➡️ Bernhard Heindl – Maintenance Consultant with a passion for “leadership responsibility in workplace safety”
🎯 What to expect? ✅ The Swiss Cheese Model: Why safety is more than following rules and why you also have it in your hands. ✅ Change Management: From “It doesn’t work for us” to “Employees demand it” ✅ Practical insights: How digital release certificates (directly from the CMMS) revolutionize acceptance. Creating acceptance in the release process – through change management, communication, and digitization ✅ Leadership responsibility: Why “the fish starts to stink from the head”
📌 Special Highlight: Experience emotional safety films by filmmaker Leonhard Lindner, showing how to convey “seemingly dry” safety topics in a gripping way and anchor them sustainably in memory!
Summary
- Introduction and Welcome: Marcel welcomed the participants of the expert breakfast and presented the formal aspects of the event. He announced the upcoming dates and events.
- Introduction of Guests: Jens introduced the guests Robin Engelmann and Bernhard and explained their backgrounds and expertise in workplace safety.
- Introduction Video: Jens showed an introductory video on workplace safety and the Swiss Cheese Model to illustrate the importance of safety layers.
- Behavioral-Based Workplace Safety: Bernhard and Robin explained the importance of behavioral-based workplace safety and the role of leaders. Robin emphasized that leaders must take responsibility and be role models.
- Leaders: Robin emphasized that leaders play a central role in workplace safety. They must take responsibility and act as role models to convey the importance of safety measures.
- Responsibility: Robin explained that many leaders believe that workplace safety is the task of the safety specialist. He emphasized that leaders must actively engage and live the measures themselves.
- Examples: Robin gave examples from his professional experience to illustrate the importance of behavioral-based workplace safety. He mentioned that technical measures are often easier to implement than organizational and personal measures.
- Coverdale Target: Robin presented the Coverdale Target as a tool to convey the meaning and importance of workplace safety measures to employees. He emphasized the involvement of employees in the process.
- Tool Presentation: Robin presented the Coverdale Target, a tool that helps convey the meaning and importance of workplace safety measures to employees. He explained that the tool can be used in shopfloor meetings to involve employees.
- Involvement: Robin emphasized the importance of involving employees in the workplace safety process. He explained that employees are often not asked and measures are imposed on them, leading to resistance.
- Example: Robin gave an example from his professional environment where the introduction of a work release system initially met with resistance. By involving employees and explaining the meaningfulness of the measures, acceptance could be increased.
- Discussion on Bureaucracy: Jörg and Robin discussed the bureaucracy and effort associated with workplace safety measures. They agreed that bureaucracy should be reduced to increase efficiency.
- Bureaucracy: Jörg and Robin discussed the high bureaucratic effort associated with workplace safety measures. Jörg criticized that qualified employees have to undergo basic safety instructions every year, which is inefficient.
- Training Tools: Robin mentioned that they are introducing a training tool to increase efficiency. The tool is intended to facilitate visitor management and training for employees and external companies.
- Efficiency: Jörg emphasized that bureaucracy impairs the efficiency of employees and that the focus should be on core tasks. He suggested reducing unnecessary regulations.
- Bradley Curve: Bernhard presented the Bradley Curve to illustrate the development of corporate culture in workplace safety. He explained the different stages and their significance.
- Curve Explanation: Bernhard presented the Bradley Curve, which illustrates the development of corporate culture in workplace safety. The curve shows four stages: instinct, rule monitoring, sensitization, and commitment.
- Stages: Bernhard explained the four stages of the Bradley Curve: 1. Instinct - Accidents are normal, 2. Rule Monitoring - 0 accidents are unrealistic, 3. Sensitization - 0 accidents are possible, 4. Commitment - 0 accidents as a commitment.
- Responsibility: Bernhard emphasized that the responsibility for workplace safety in the higher stages of the curve lies with the employees themselves. In the highest stage, employees look out for each other and take responsibility for themselves and others.
- Fluctuation and Language Diversity: Peter Mühl addressed the challenges posed by high fluctuation and language diversity. Marcel and Robin discussed possible solutions, such as training tools and videos in different languages.
- Challenges: Peter Mühl addressed the challenges posed by high fluctuation and language diversity. He mentioned that this complicates workplace safety and communication within the company. Training Tools: Robin and Marcel discussed possible solutions to address the challenges. They suggested using training tools and videos in different languages to better reach employees.
- Use of AI: Robin mentioned that they use AI to translate training videos into different languages. This is intended to ensure that all employees understand and follow the safety instructions.